Justifying Headcount
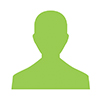
Forum Friends:
How do you justify additional/replacement headcount in your organization? Just wondering if it's a fly-by-the-seat-of-your-pants thing most places or if it involves mathmatical equations and lines of approval, etc. If you feel you already have too much "dead weight" but the organization keeps hiring, what as an HR professional can you do to help solve this issue?
I have a friend who is drowning in this type of situation right now and I don't know what to tell her. I suggested running reports from the payroll data (no HRIS available) to see what dept's are costing, what the average ee costs to "carry" and use that type of data to show the execs the kind of dough that's being spent on the dead-weights. Any other suggestions?
How do you justify additional/replacement headcount in your organization? Just wondering if it's a fly-by-the-seat-of-your-pants thing most places or if it involves mathmatical equations and lines of approval, etc. If you feel you already have too much "dead weight" but the organization keeps hiring, what as an HR professional can you do to help solve this issue?
I have a friend who is drowning in this type of situation right now and I don't know what to tell her. I suggested running reports from the payroll data (no HRIS available) to see what dept's are costing, what the average ee costs to "carry" and use that type of data to show the execs the kind of dough that's being spent on the dead-weights. Any other suggestions?
Comments
She just needs to look for points of comparison with the information she has available & be creative (but accurate). I recently had a clerical person in one of our offices who kept demanding that she needed a whole department of additional clerical help (reporting to her, of course). I didn't want to prove my point with revenue, because her supervisor doesn't see that info. So I calculated a ratio of clerical hours/client (clients is a measure of our workload). This ratio demonstrated that, compared to the other offices, she was not overworked at all...just inefficient. I liked that ratio so well that I'm going to add it to my metrics for all our offices. It was a very revealing measure of efficiency.
I'm a big fan of metrics. Without them, you have no objective measure to judge by.
An additional way of calculating is cost of widgets (production) produced verses gross $ollars spent to get out one widget or 100s of widgets.
We look at the total number of hours spent to produce a "piglet" which goes to market. Once we have the total Gross payroll dollars spent to get a total number of widgets shipped, then one can find out the true value of the hours worked and the $ollars spent to get the total widgets produced.
TOTAL GROSS PAYROLL/BY THE TOTAL NUMBER HOURS SPENT = COST OF WORKING HOURS.
TOTAL GROSS PAYROLL /BY THE TOTAL NUMBER OF WIDGETS PRODUCED = COST OF EACH WIDGET PRODUCED.
Every piglet produced this week cost in labor dollars was $12.79 per hour. The high work site was $29.74 per hour worked and the low work site was $9.83 per hour worked. The most efficient unit out did the worst by 400 piglets during this week.
Every piglet produced this week cost $5.11 in labor $OLLARS. The high work site was $14.18 per piglet produced and the low was $3.26 per piglet produced.
You can divide whatever $ollar cost into the production arena and value manpower as we do. If you are a service company find out your number of widgets, bank statements, or whatever produced that is the core of the business and divide the production by the expense to get the production and you can evaluate the efficiency of the people or group of people.
HOPE this helps. The production group were amazed when I first produced this standard chart. Once they understood it then they tried to get it destroyed, but the General kinda liked it and the owners now get their detailed weekly report and will ask questions when something appears to be going off the track!
PORK
Our maintenance team is a highly skilled unit with high payroll cost even though it only has 15 person. We take their personnel labor cost (GROSS) and divide it by 15 and we can watch each week how the effect of overtime drove up the cost; We can then then add this unit to the production unit and we can see the impact on this group's participation drove up the cost of one piglet. Feedmill produces and knows exactly what the cost of feed per lb is and they use that figure to assess their personnel cost.
One only needs to set a standard to "eval from" and they can decide if the unit is over strength or understrength. Overtime will tell you if your unit is under staffed or is the individual using the clock to increase their pay. When your weekly production includes 60 hours of o/t then, if true, the unit most likely needs an additional 1 1/2 person to get the hours spent down 40 of the 60 would be allocated to 1 person and the 20 additional hours would be controlled by the supervisor/manager. Your cost will go down by adding another person because the 20 hours of O/T cost is 1 1/2 times the cost of 1 person.
PORK