Calling all Manufacturing Companies!!
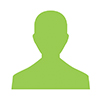
Hi Everyone,
Here is the background: We are a chemical company who handles raw materials in pails and 55 gallon drums. Our QA Inspectors are required to take samples as part of their routine job duties. Recently, we've seen an increase in workplace incidents and during our investigation found that they are performing material handling i.e.; moving drums, etc.
The Manager for that department says that is what everyone else in the industry does. We [HR] says that they shouldn't be performing these tasks.
Who is right? The Manager or HR? How do your QA Inspectors take samples. Your input (as well as any SOP's) would be greatly appreciated as we want to change the way samples are taken so as to remove the possibility of workplace injuries.
Thanks!!!
LFernandes, NY
Here is the background: We are a chemical company who handles raw materials in pails and 55 gallon drums. Our QA Inspectors are required to take samples as part of their routine job duties. Recently, we've seen an increase in workplace incidents and during our investigation found that they are performing material handling i.e.; moving drums, etc.
The Manager for that department says that is what everyone else in the industry does. We [HR] says that they shouldn't be performing these tasks.
Who is right? The Manager or HR? How do your QA Inspectors take samples. Your input (as well as any SOP's) would be greatly appreciated as we want to change the way samples are taken so as to remove the possibility of workplace injuries.
Thanks!!!
LFernandes, NY
Comments
You might want to check the OSHA site and see if your employees are required to be specially trained to handle your specific chemicals. In any case, increased accidents surely would indicate that there's a problem with the way things are being done now.
Good luck.
We do the training (both written and practical)using a modified NSC program, and publish a list of those "certified" to drive. Our former corporate safety director used to issue actual certificates but I don't have time. You're right about the licenses - we don't issue them as documents but we have been asked to prove that our drivers are licensed in the sense of being properly trained. It is definitely a violation to let an untrained employee drive your forklifts and you'd better have the training documented somehow if OSHA comes calling.
Sorry for the confusion.
LFernandes
While HR/Safety states that this individual should not be performing the job of moving drums, the Manager states that QA inspectors are expected to.
So the question is:
Who is correct... HR or the Manager. That was why I was asking other manufacturers if they require their QA Inspector to handle drums. If that is the case, then we should be providing them with the proper training.
Hope this helps...
LFernandes
Teach the proper lifting techniques and stress that if something is too heavy to lift, get help. The manager should be behind that. If somone gets hurt they are worse off than if the QA person slows down and asks for help.
To answer your question...YES!!...UNLESS it is part of their routine job duties which is why I am trying to find out if other manufacturing companies have their QA Inspectors moving drums. AND... should that be the case, it will be written in as part of the job description that they must be able to lift up to 100 pounds on a routine basis. Right now, the job description has them lifting 10. Which is a Big difference.
LFernandes
So, to me, it's not a question of what the QA inspector's job description should be. It's a question of whether you hold the workforce accountable, and part of the accountability is positioning a full 55 gallon drum properly on a work surface or pallet. The same would hold true if a pallet were in a walking path. Or if a box of finished goods happened to be out of place. Hold people accountable. Yo momma don't work here!
If we could harness the amount of energy that has gone into this exchange, we could move a 550 lb barrell.
We keep our job descriptions as vague as possible. Most of our facilities only list physical requirements for an area with listing specific duties. Why? Everyone is expected to do whatever it takes to get the job done. All people in a department have the same physical requirements so everyone can do each others work without question as to physical ability or ADA crap.
When we see something wrong, we fix it. We would never question a job description. I would tell your QA people to learn the proper technique. I'd do as Don said and hold your material handlers accountable. And I'd certainly stop questioning, "Who is right?" Everybody should take Nike's advice and just do it.
If I were in charge of safety at that facility, I would walk out on the floor and begin straightening barrels to immediately show people how to do it.
I hate to create any tie to SMACE, but I will. Good comments on HR's role. Please, just do it.
E Wart
Employees who see managers and others coming along tidying up their messes and covering their mistakes will soon adopt the notion that "I'm not going to be held accountable. My momma gonna straighten this mess up for me". Safety in a manufacturing facility nudges bottom line profit for the number one position.
Where I work, we insist on and demand safe practices and we write up and terminate employees for safety violations. What we do not do is walk around behind people cleaning up their oil slicks, turning off their towmotors, straightening their misplaced drums, teaching them that others will cover for their breaches and preaching the 'everybody's responsible for it' philosophy. I can either straighten the barrel for the unsafe worker who left it there, or I can put a string of yellow tape around it, go get his supervisor and let him handle the writeup. If it saves a comp accident, the 15 minutes spent on it is worth gold!
Where accountability can't be assigned and traced to the lowest common denominator, nobody is held accountable. And where there's no accountability there's no safety discipline in place. And barrels are leaning off pallets. Call it Safety/OSHA Crap if you like. The cost of Workers' Compensation premiums, accident costs and OSHA fines demand a pretty damned high level of attention. Sorry, just a different take on the subject. Readers can choose whichever best fits their company culture.
I said Just Do It and hold people accountable. The original poster seemed to understand this.
Do we have to go down this long and bumpy road of listing all of the obvious...wc, OSHA fines, etc...blah blah blah...all so obvious.
Get rid of work distinctions as much as possible. When you do this, its amazing how well employees hold each other accountable. Ands when they don't, immediately hold them accountable.