Timing Process
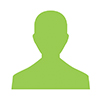
[font size="1" color="#FF0000"]LAST EDITED ON 05-14-03 AT 07:31AM (CST)[/font][p]I am hoping someone out there could help me or guide me to the right direction. Our manufacturing facility requires our entry level position to assemble a certain number of products. For example an employee must produce in a minute 25 products. Are there any legal ramifications in timing an employee to ensure productivity does not drop? We find the employees slack off if not timed. Anyone out there has a similar process and how do you ensure the actual timing is done accurately and consistenly? Your comments and feedback are much appreciated.
Comments
As far as legalities, I haven't run into anything that tells me this is illegal.