Safety Committees??
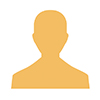
How many of my fellow Forum members have safety committees? If so, how are they structured (exempt and non-exempt employees, only non-exempt, etc.)? Do you feel the structure you have works? If so, why? If not, why not?
Another question, how do you promote safety at your company? Prizes? Rewards? Time off?
Think that I have listed enough questions for one thread? I agree. Thanks for your input!
Another question, how do you promote safety at your company? Prizes? Rewards? Time off?
Think that I have listed enough questions for one thread? I agree. Thanks for your input!
Comments
We have quarterly walk-a-rounds and also show safety videos from time to time to promote safety. You can rent videos free from OSHA or often from your WC insurer.
[email]paulknoch@hotmail.com[/email]
Paul-What do you mean by "We follow OSHA guidelines for how the committee is weighted with management/non-management staff."? Am I missing something? Are we required to have non-management staff as part of our safety committee?
I believe safey incentives work but they have to be closely monitored and clearly explained.
We do not currently have awards programs. We have the running debate of whether it would make people not report things vs. it would create more awareness. Each member has a t-shirts with company name and 2002 safety committee so that other employees are aware of who members are. We do not require them to wear them or to wear at any certain time.
our best safety incentive is we have a lost time poster that says how many days we have gone without a lost time accident. for some reason, no one wants to be the one to make the numbers go back to zero. we have gone a couple of years now without a lost time accident. we have had a few minor accidents, but no lost time accidents. We did a few pizza parties to recongize what a great job the employees have been doing at staying safety conscience. food is always appreciated!
We are a small manufacturing site and we do have a pro-active safety team (committee). We have one manager on the team who is the Safety Administrator, one office employee, and four production (union) employees from various departments.
The safety team has input into the monthly safety training performed at our site. It also performs the monthly safety audits of the site, develops occasional safety contests, and helps decide on what safety incentive programs will be presented each year.
This year (and last) we give a $10 Walmart gift certificate each quarter to every employee when the company as a whole passes the monthly safety audit for the quarter. This is based on a calendar quarter. And when we have had no last-time accidents for 90 days we take everyone out to lunch. Our employees really seem to like both of these programs and our safety incidents have decreased significantly over the last four years.
Each year we hold a health fair as part of our Wellness Program. The Safety Committee serves breakfast that morning to anyone attending the health fair.
After an employee has served on the commitee for their term, they receive a gift. (Last I knew it was a large flashlight) We also have a plaque on the wall with all commitee's names on it for each year.
We try to send our committees to some sort of training while they are in term. The committee has been a great asset to our cooperative. I would recommend forming one to anyone.
K.Olson
To make matters even more interesting we are located in a ski resort and one of our companies operates a variety of transportation lifts. The ski industry historically experiences a high rate of worker's comp injuries and associated claims costs.
We implemented a safety committee for several reasons. We wanted to facilitate healthy interaction between the employees of each company. We wanted to empower the employees to take the responsibility for their own safety and that of their co-workers and our guests. We wanted to facilitate a decline in our sky rocketing worker's comp costs.
Our safety committee has accomplished all of the above. It is composed of front line employees, most of whom are non-exempt personnel. Every department in all three companies has a safety committee representative and the committee meets a minmum of once per month to examine issues of their own choosing. They also review injuries and do their own investigations when necessary.
Our safety committee has implemented a safety rewards program. Each month, every employee in every injury free department receives a $10 coupon. The departments who do not receive these rewards have experienced decreased workers comp claims. The cost of the reward program is minimal compared to the saving we are seeing.
Our intent was for employees to take ownership of their safety. It is their responsibility to stay safe.
We did have a monetary safety incentive to reward quarters with no accidents, but this was discontinued this year due to budget cuts. We still have a drawing for 5 free floating holidays (1 day for each of 5 winners) and 5 winners of a gift (ie: T-shirt, flashlight, travel mug, 6-pack cooler, etc.). In order to be eligible for this drawing you need to have attended all 3 safety meetings in the quarter. Our focus is on training and attending the meetings.
If you need any more info, please e-mail me at [email]fountain.carla@ocls.info[/email]